For pumps connected in serial - add head, for pumps connected in parallel - add flowrates
- Capacitor In Series And Parallel
- Pumps In Series And Parallel Pdf To Doctor
- Pumps In Series And Parallel Pdf To Doc Converter
Capacitor In Series And Parallel
Pumps can be arranged and connected in serial or parallel to provide additional head or flow rate capacity.
Pumps in Serial - Head Added
Pumps operating in series or parallel are pretty simple. When operating in series flow remains the same as a single pump but head is doubled at each flow point. In parallel operation head remains the same as a single pump but flow is doubled at each head point. Figure 1 illustrates these rules. The blue curve is the one. These preceding concepts are absolutely crucial to understanding many of the issues associated with operating pumps in parallel. PIA President Regular readers of Pump Industry will be familiar with Ron Astall’s popular series of. New pump stations connected in Port Macquarie-Hastings Tender: sewerage works in Gympie. Email * Featured Video. Learn how operating centrifugal pumps in series or parallel can help you reach system operating requirements. The following post walks you through pumps in series and in parallel so that you can get your ducks I mean pumps in a row – or side by side, depending on the application. In situations where a high, constant pressure is. H83 Two-Stage (Series and Parallel) Pumps For a comprehensive range of investigations into the operation and characteristics of a single centrifugal pump, and two centrifugal pumps in both series and parallel fluid mechanics • Self-contained, mobile two-stage centrifugal pump test set for a range of tests and demonstrations. This tutorial is intended for anyone that has an interest in centrifugal pumps. There is no math, just simple explanations of how pump systems work and how to select a. Centrifugal pump? - How to do details calculations that will allow you to size and select a centrifugal. Series 90 variable displacement pumps are compact, high power density units. All models utilize the parallel axial piston/slipper concept in conjunction with a tiltable swashplate to vary the pump’s displacement. Reversing the angle of the swashplate reverses the flow of oil from the pump and thus reverses the direction of rotation of the motor output.
When two (or more) pumps are arranged in serial their resulting pump performance curve is obtained by adding their heads at the same flow rate as indicated in the figure below.
Centrifugal pumps in series are used to overcome larger system head loss than one pump can handle alone.
- for two identical pumps in series the head will be twice the head of a single pump at the same flow rate - as indicated with point 2.
Crash bandicoot n.sane trilogy pc download. With a constant flowrate the combined head moves from 1 to 2 - BUT in practice the combined head and flow rate moves along the system curve to point 3.
- point 3 is where the system operates with both pumps running
- point 1 is where the system operates with one pump running
Note that for two pumps with equal performance curves running in series
- the head for each pump equals half the head at point 3
- the flow for each pump equals the flow at point 3
Operation of single stage pumps in series are seldom encountered - more often multistage centrifugal pumps are used.
Pumps in Parallel - Flow Rate Added
When two or more pumps are arranged in parallel their resulting performance curve is obtained by adding the pumps flow rates at the same head as indicated in the figure below.
Centrifugal pumps in parallel are used to overcome larger volume flows than one pump can handle alone.
- for two identical pumps in parallel and the head kept constant - the flow rate doubles compared to a single pump as indicated with point 2
Note! In practice the combined head and volume flow moves along the system curve as indicated from 1 to 3.
- point 3 is where the system operates with both pumps running
- point 1 is where the system operates with one pump running
In practice, if one of the pumps in parallel or series stops, the operation point moves along the system resistance curve from point 3 to point 1 - the head and flow rate are decreased.
Note that for two pumps with equal performance curves running in parallel
- the head for each pump equals the head at point 3
- the flow for each pump equals half the flow at point 3
Note - for parallel operation
- zero flow or “shut valve” heads must match for the pumps
- unstable pump curves must be avoided
- steeper pump curves are preferred
Related Topics
- Pumps - Piping systems and pumps - centrifugal pumps, displacement pumps - cavitation, viscosity, head and pressure, power consumption and more
Related Documents
- Alternating Pumps - Securing a system and achieve equal wear by alternating pumps in parallel
- Centrifugal Pumps - An introduction to Centrifugal Pumps
- Pipes - in Series or Parallel - Pressure loss in pipes connected in series or parallel
- Positive Displacement Pumps - Introduction tutorial to positive displacement pumps basic operating principles
- Pumping Water - Energy Cost Calculator - The energy costs of pumping water
- Pumping Water - Required Horsepower - Horsepower required to pump water
- Static Pressure vs. Head in Fluids - Static pressure and pressure head in fluids
- System Curve and Pump Performance Curve - Utilize the system curve and the pump performance curve to select the proper pump for a particular application
Tag Search
- en: pumps parallel series
- es: bombas serie paralela
- de: Pumpen parallel Serie
- About this Journal ·
- Abstracting and Indexing ·
- Aims and Scope ·
- Article Processing Charges ·
- Bibliographic Information ·
- Editorial Board ·
- Editorial Workflow ·
- Publication Ethics ·
- Reviewer Resources ·
- Submit a Manuscript ·
- Subscription Information ·
- Annual Issues ·
- Open Special Issues ·
- Published Special Issues ·
Experimental Study on Series Operation of Sliding Vane Pump and Centrifugal Pump
Department of Petroleum Supply Engineering, LEU, Chongqing 400016, China
Received 19 June 2013; Revised 3 September 2013; Accepted 4 September 2013
Academic Editor: Ryoichi Samuel Amano
Copyright © 2013 Tao Li et al. This is an open access article distributed under the Creative Commons Attribution License, which permits unrestricted use, distribution, and reproduction in any medium, provided the original work is properly cited.
Abstract
A platform for sliding vane pump and centrifugal pump tests is installed to study the series operation of them under different characteristics of pipeline. Firstly, the sliding vane pump and the centrifugal pump work independently, and the performance is recorded. Then, the two types of pumps are combined together, with the sliding vane pump acting as the feeding pump. Comparison is made between the performance of the independently working pump and the performance of series operation pump. Results show that the system flow rate is determined by the sliding vane pump. In order to ensure the stability of the series operation pumping system, the energy consumption required by the pipeline under the system flow should be greater than the pressure energy centrifugal pump can generate. Otherwise, the centrifugal pump can not operate stably, with reflux, swirl, gas-liquid two-phase flow in the runner and strong vibration and noise. The sliding vane pump can be in serial operation with the centrifugal pump under limited conditions.
1. Introduction
In china, some oil devices are equipped with sliding vane pumps (such as the fixed refueling vehicles), and some are equipped with centrifugal pumps (such as the delivery pumps in oil pipeline). In order to complete the mission of transporting oil for emergency, there is a strong demand for combining these equipments together under current equipment system, thus leading to the series operation of the two types of pumps.
However, the working principles of sliding vane pump and centrifugal pump are completely different. The former belongs to positive displacement pumps, while the latter belongs to dynamic pumps [1, 2]. The series, parallel, and series-parallel operations of centrifugal pumps are widely used [3–5]. Relatively, there are rare reports and research literatures on the series operation of sliding vane pumps and the two types of pumps. According to the working performance of sliding vane pump, Daniel and Wordley [5] put forth the concept that it is not necessary to run pumps in series because a positive displacement pump will be self-compensating for system pressure and will only move a specific number at a given rpm, besides there is no advantage to place positive displacement pumps in series when they are in close proximity to each other. Karassik and Messina [1] presented an idea on the issue of series operation of positive displacement pump and centrifugal pump that it would be most unusual to encounter a positive displacement pump feeding into the suction of a centrifugal pump because of the high pressure that could be imposed on the centrifugal pump suction and because of the amplification of flow pulsations resulting from interaction of the characteristics of the two pumps, which could be deleterious to both pumps, yet with no experimental verification.
In order to investigate the series operational properties of them and guide their application, an experimental platform is designed and installed [6]. Firstly, the independent working characteristics of two selected pumps are tested. Then, they are tested in series operation to study and analyze the characteristics and regularity of their series operation.
2. Performance Tests of Sliding Vane Pump and Centrifugal Pump
2.1. The Experimental Process and Equipments
The experimental process and equipments of the independent operation of sliding vane pump and centrifugal pump are shown in Figure 1 and Table 1.
Jul 21, 2013 Cara Hack Password Rar dan Zip Online 2013 (No Download 100% Work) 01:48 BELAJAR, TIPS DAN TRIK 6 comments S eringkali jika kita mendownload sebuah file dari internet tak jarang kita menjumpai file yang tersimpan di format.rar alasan banyak file di tempakan di rar adalah untuk melindungi file tersebut dari serangan firus atau sesuatu yang dapat merusak file tersebut. Jun 22, 2016 ou will need to crack ZIP password in many situations, such as when you forget your ZIP file password, lost it, get a ZIP file from others without knowing its password etc. Tenang, JalanTikus akan berikan cara hack file RAR yang dikunci password! Siapa yang tidak kenal file RAR? Bagi pengguna komputer, kamu pasti akrab dengan jenis file yang bisa melakukan k ompresi data dari ukuran besar menjadi lebih kecil ini. Cara hack password file extensi zip android. Baca Juga: Cara Membuat File Torrent Menggunakan uTorrent Dengan Mudah. Sebelum dilanjut sebenarnya apa sih file RAR itu? File RAR adalah sebuah file yang awalnya telah dikompresi (arsip) menggunakan software WinRAR. Selain file RAR, software WinRAR juga bisa membuat file ZIP. Dengan WinRAR kita bisa membuat ukuran file (kapasitas) menjadi lebih kecil.
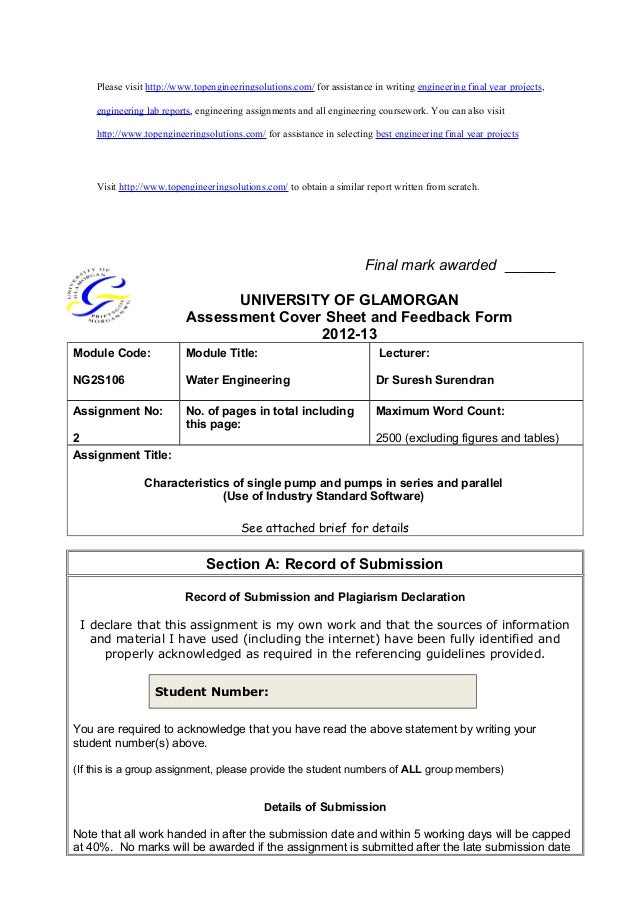
2.2. Drawing of Performance Curves
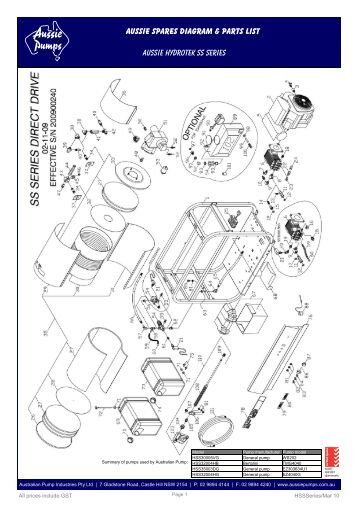
To take a sliding vane pump at a rotational speed of 1490 r/min and a centrifugal pump at 2940 r/min, for example, through the parameters gained from the experimental records and calculation, the performance curves of two pumps are drawn (Figures 2 and 3). For the convenience of later comparative analysis, the differential pressure of centrifugal pump is used rather than the head capacity.
3. Experiment on Series Operation of Sliding Vane Pump and Centrifugal Pump
3.1. The Experimental Process
Based on the above single pump experiment, an experiment on the series operation of sliding vane pump and centrifugal pump is adapted, as shown in Figure 4. The pressure transmitter collects the pressure values on the inlet and outlet of sliding vane pump, the interposition of the series pipelines of two pumps, and the inlet and outlet of centrifugal pump, respectively, while flow transmitter collects the flow values of the outlet of these two pumps, respectively. The collected data are acquired and integrated on the DAQ board and recorded by a PC.
3.2. The Experimental Methods and Steps
3.2.1. Experiment I
(1) Shut down the by-pass butterfly valve, open all the gate valves in pipeline, start data collection at 0 s, and start the sliding vane pump at 9 s.
(2) After the system is running steadily, open centrifugal pump at 140 s, and the two pumps operate in series. Shut down the centrifugal pump and sliding vane pump at 1012 s and 1046 s successively. Stop data collection at 1060 s.
(3) Open the sliding vane pump and centrifugal pump again. When the two pumps operate in series, open the butterfly valve of the by-pass pipeline on the outlet of centrifugal pump. Observe the liquid flow through sight glass.
3.2.2. Experiment II
(1) It is the same as Step 1 in experiment I.
(2) When the liquid flow is stable, start the centrifugal pump (at 98 s). The two pumps then operate in series. When the pressure of centrifugal pump outlet is stabilized at 0.02 MPa, adjust valve 19 of centrifugal pump outlet (at 260 s) to change the pipeline friction loss. Narrow down the opening of valve 19 to increase the outlet pressure of centrifugal pump by 0.05 MPa each time until the valve is fully closed (1764 s). The outlet pressures of centrifugal pump and its corresponding time are shown in Table 2.
(3) Open gate valve 19 quickly until it is fully opened, and stop the centrifugal pump and sliding vane pump, stop data collection.
3.3. Results and Analysis
3.3.1. Results and Analysis of Experiment I
In experiment I, the system is stable when the sliding vane pump is working alone. All parameters have good stability. But after the centrifugal pump is turned on, the centrifugal pump and its pipeline begin to vibrate and obvious noise and severe calorification can be observed. The changes of all parameters are shown in Figures 5 and 6. Then, it can be observed that a lot of bubbles flow out from the pipeline to sight glass in Step (3), which suggests that the liquid in centrifugal pump is being vaporized. So, there is a two-phase flow of liquid and gas within centrifugal pump and the pipeline behind it.
As shown in Figure 5, when sliding vane pump is turned on, quickly falls to −0.047 MPa, and , , and quickly rise to 0.264, 0.256, and 0.235 MPa. rises to 0.02 MPa. At 140 s, the centrifugal pump is opened. slightly falls down while , , and significantly drop to −0.049, −0.058 and −0.077 MPa. slightly increases. In series operation, all pressures basically remain the same. At 1012 s, shut down the centrifugal pump. Yu gi oh a duel with dartz. All the parameters return to the independent working state of sliding vane pump. Shut down the sliding vane pump. All the parameters return to original state.
As shown in Figure 6, when sliding vane pump is opened, rises to 0.31 MPa immediately. All the energy consumed is borne by sliding vane pump. At this moment, centrifugal pump is the leading energy consumption of system. The pressure drops to 0.22 MPa after passing the centrifugal pump. is the same as at 17.7 m3/h. At 140 s, the centrifugal pump is opened. immediately reduces to −0.002 MPa. increases to 0.1 MPa rapidly, and the two exchange their roles as energy consumer and provider. increases slightly to 18.5 m3/h under the fixed speed because of the declination of . The value of is bigger than . This is because the evaporation of liquids takes place after reaching the centrifugal pump. Within the fixed volume of pipeline, a large amount of gas reduces and compresses the volume of liquid, thus leading to the increase of the flow velocity which is proportional to the value of flow sensor. However, the pure liquid flow of system is . and basically remain the same during the series operation.
Compared with the independent working condition of the two pumps, the flow and differential pressure changes of the sliding vane pump follow the rule which is suggested in Figure 2 whether it works independently or operates in series with the centrifugal pump. However, the differential pressure of the serial centrifugal pump is only 0.1 MPa when the flow is 18.5 m3/h which significantly deviates from the differential pressure 0.43 MPa when centrifugal pump works independently under the same flow shown in Figure 3. The serial centrifugal pump receives the dual effect of both the sliding vane pump and the characteristics of the pipeline. The flow is determined by the preceding-stage sliding vane pump, and the differential pressure is influenced by the characteristics of the pipeline. The centrifugal pump itself can provide the energy amounting to 0.43 MPa which is much bigger than that needed by the pipeline. Therefore, the complex and unstable flow will be resulted inside the centrifugal pump to offset the superfluous energy in order to maintain the balance between supplies and demands. The energy loss appears in the form of reflux and swirl [7, 8]. The stronger the reflux is, the bigger the volume of the swirl is and the greater the energy loss is. Moreover, it will lead to the pulsation of flow and pressure, which will further lead to vibration and noise. That is why there is vibration and noise in the experiment.
Pumps In Series And Parallel Pdf To Doctor
3.3.2. Results and Analysis of Experiment II
Based on experiment I, we close the outlet valve of the centrifugal pump gradually to make a further study in experiment II. The variation of the system parameters in the experiment is shown from Figures 7 to 8.
Pumps In Series And Parallel Pdf To Doc Converter
The working status of the system before closing the outlet valve and after opening the outlet valve is the same as that in experiment I. So, emphases are put on the dynamic variation regularity of each parameter during the valve closing process in experiment II. The outlet valve of the centrifugal pump is closed gradually with as reference standard. Figure 7 shows the periodic rise of while the valve is closing. When the valve is completely closed, the pressure rises to its maximum value of 1.19 MPa. At the points of 0.17, 0.22, and 0.27, fluctuates greatly. From 260 s to 702 s, the variation trends of , , and are consistent with each other and with little variation. Between 702 s and 1764 s, , , and increase apparently and reach respective peak value at 1764 s when the liquid flows back completely through the safety valve.
is stable at first and then begins to increase. The value remains basically unchanged from 260 s to 702 s. From 702 s to 1285 s, the increase is slow. From 1285 s to 1764 s, the increase is significant. At 1764 s, it reaches the peak of −0.030 MPa.
Figure 8 is the variation trend of the flow and differential pressure in experiment II. The value of is still greater than that of during 98 s and 272 s. After further turning down the valve, and gradually become consistent. The variation of parameters during valve closing process can be classified into three periods. Comparison is made between the performance in series operation and the performance in independent operation which is shown in Figures 9 and 10. In the first period (from 260 s to 702 s), shows little change, staying at −0.003 MPa. The stable working condition of the sliding vane pump enables to maintain around 18.5 m3/h, while keeps surging with the flow remaining unchanged, which reaches 0.43 MPa at 702 s. Besides, the working status of the centrifugal pump is quite unstable with the pressure ranging from 0.2 MPa to 0.3 MPa. At this period, the differential pressure of the centrifugal pump is still less than that when it works independently under the same flow (Figure 10) which further validates its abnormal operation state. In addition, the fierce unsteady flow within the pump and pipe changes the velocity and pressure distribution of liquid in the runner. This remarkably reduces the efficiency, degrades the performance, and shortens the lifespan of the centrifugal pump. The change in the characteristics of the pipeline has no direct impact on the sliding vane pump. But the centrifugal pump makes a response and comes close to a stable working status. In the second period (from 702 s to 1285 s), keeps rising and reaches the rated differential pressure of the safety valve of 0.4 MPa at 1285 s. The flow rate reduces from 18.5 m3/h to 17.4 m3/h slowly. rises slowly from 0.43 MPa to 0.44 MPa due to the decrease of the system flow rate. At this period, in the case that the centrifugal pump works steadily and that the safety valve of the sliding vane pump does not open, the change in the characteristics of the pipeline exerts a major impact on the sliding vane pump. Therefore, the system flow rate has minor change. The centrifugal pump works steadily under the flow. In the third period (from 1285 s to 1764 s), increases gently compared with the second period. The opening of the safety valve and the increasing cause the decrease of . The steady declining changes into ladder-formed declining, and at 1764 s, it reduces to 0 m3/h. rises because of the declining of , and the rising trend is more stable than the first period. We can see that once the sliding vane pump’s safety valve opens, the change in the characteristics of the pipeline will result in great change in the working parameters of the two pumps as well as the flow.
3.4. Conclusions
Through the analysis and comparison of the results in experiment I and experiment II, the following conclusions can be drawn.
(1) The system flow rate is determined by the characteristics of the feeding sliding vane pump. The working performance of the two pumps and the characteristics of the pipeline are crucial for normal and steady system operation. In the serial use, the corresponding relation between the system flow and the differential pressure of the sliding vane pump fits its independent working characteristics well. The operation of the centrifugal pump effectively changes the differential pressure of the sliding vane pump by sharing the pressure energy of the system, thus leading to the change in the system flow.
(2) The centrifugal pump works under the flow determined by the sliding vane pump. If the energy it provides is larger than the energy consumed by flow, then fierce unsteady such as reflux, swirl, gas-liquid two-phase flow will occur inside the centrifugal pump to consume the superfluous energy.
(3) During different periods, the change of the pipeline characteristics has different impacts on the working status of the two pumps. When the centrifugal pump is under abnormal operation, changing the pipeline friction loss causes nearly no sliding vane performance variation and no flow rate change. The centrifugal pump changes the operation parameters and slowly comes near to or far away from the normal working status. After the centrifugal pump works steadily and before the safety valve opens, the change in the characteristics of the pipeline exerts a major influence on the operation of the sliding vane pump. As a consequence, the system flow has a small-scale change. After the safety valve opens, both of the two pumps change the operation parameters to adapt to the change in the characteristics of the pipeline.
4. Summary
Series operation experiments for sliding vane pump and centrifugal pump are conducted. Sliding vane pump is used as the preceding-stage pump and the centrifugal pump as the secondary pump. By changing the friction loss of the pipeline, results are gained under different operational conditions. Experimental results show that the system rate of flow is determined by the sliding vane pump. The centrifugal pump works under the flow rate restricted by the sliding vane pump. Only when the friction of the pipeline is greater than the pressure energy that the centrifugal pump can provide, the system can operate normally. Otherwise, the system will work unsteadily with calorification, vibration, and noise. So, the sliding vane pump can be in serial operation with the centrifugal pump under limited conditions.
Acknowledgment
This paper is supported by the Academic Innovation Fund of Logistical Engineering University.
References
- I. J. Karassik and J. P. Messina, Cooper Paul, and Heald C. C.Pump Handbook, McGraw-Hill, New York, NY, USA, 3rd edition, 2001.
- J. F. Gulich, Centrifugal Pumps, springer, New York, NY, USA, 2007.
- J. Yuan and S. Yuan, “Prediction of performance for dissimilar centrifugal pumps coupled in series or in parallel,” Drainage and Irrigation Machinery, vol. 22, no. 6, pp. 1–4, 2004.View at Google Scholar
- E. da Costa Bortoni, R. A. Almeida, and A. N. C. Viana, “Optimization of parallel variable-speed-driven centrifugal pumps operation,” Energy Efficiency, vol. 1, no. 3, pp. 167–173, 2008.View at Publisher · View at Google Scholar · View at Scopus
- U. C. Daniel and M. Wordley, “A comparison of the application of centrifugal and positive displacement pumps,” in Proceedings of the 17th International Pump Users Symposium, pp. 145–152, 2005.
- C. Wu, J. Chen, and B. Chen, “Design and application of performance test bed for sliding-vane pump,” Petrochemical Equipment, vol. 39, no. 1, pp. 14–16, 2010.View at Google Scholar · View at Scopus
- S. Yuan, Y. Liang, J. Yuan, J. Zhang, and Y. Luo, “Numerical simulation and experiment on characteristics of centrifugal pump inlet recirculation,” Journal of Drainage and Irrigation Machinery Engineering, vol. 29, no. 6, pp. 461–465, 2011.View at Publisher · View at Google Scholar · View at Scopus
- K. Zhang, Principle of Fluid Machinery, China Machine Press, Beijing, China, 2010.